ಸೆಲ್ಯುಲೋಸ್ ಈಥರ್, ಸೋಡಿಯಂ ಕಾರ್ಬಾಕ್ಸಿಮಿಥೈಲ್ ಸೆಲ್ಯುಲೋಸ್
ಅಂಟಿಕೊಳ್ಳುವಿಕೆಯ ಪರಿಣಾಮ
ಸ್ಲರಿಯಲ್ಲಿ CMC ಯ ಅಂಟಿಕೊಳ್ಳುವಿಕೆಯು ಹೈಡ್ರೋಜನ್ ಬಂಧಗಳು ಮತ್ತು ಮ್ಯಾಕ್ರೋಮಾಲಿಕ್ಯೂಲ್ಗಳ ನಡುವೆ ವ್ಯಾನ್ ಡೆರ್ ವಾಲ್ಸ್ ಬಲಗಳ ಮೂಲಕ ದೃಢವಾದ ಜಾಲ ರಚನೆಯ ರಚನೆಗೆ ಕಾರಣವಾಗಿದೆ.CMC ಬ್ಲಾಕ್ಗೆ ನೀರು ತೂರಿಕೊಂಡಾಗ, ಕಡಿಮೆ ನೀರಿನ ಆಕರ್ಷಣೆ ಹೊಂದಿರುವ ಹೈಡ್ರೋಫಿಲಿಕ್ ಗುಂಪುಗಳು ಉಬ್ಬುತ್ತವೆ, ಆದರೆ ಹೆಚ್ಚು ಹೈಡ್ರೋಫಿಲಿಕ್ ಗುಂಪುಗಳು ಊತದ ನಂತರ ತಕ್ಷಣವೇ ಪ್ರತ್ಯೇಕಗೊಳ್ಳುತ್ತವೆ.CMC ಉತ್ಪಾದನೆಯಲ್ಲಿನ ಅಸಮಂಜಸ ಹೈಡ್ರೋಫಿಲಿಕ್ ಗುಂಪುಗಳು ಮೈಕೆಲ್ಗಳ ಅಸ್ಥಿರವಾದ ಚದುರಿದ ಕಣಗಳ ಗಾತ್ರಕ್ಕೆ ಕಾರಣವಾಗುತ್ತವೆ.ಜಲಸಂಚಯನ ಊತವು ಮೈಕೆಲ್ಗಳ ಒಳಗೆ ಸಂಭವಿಸುತ್ತದೆ, ಹೊರಗೆ ಬೌಂಡ್ ನೀರಿನ ಪದರವನ್ನು ರೂಪಿಸುತ್ತದೆ.ವಿಸರ್ಜನೆಯ ಆರಂಭಿಕ ಹಂತದಲ್ಲಿ, ಮೈಕೆಲ್ಗಳು ಕೊಲೊಯ್ಡ್ನಲ್ಲಿ ಮುಕ್ತವಾಗಿರುತ್ತವೆ.ವ್ಯಾನ್ ಡೆರ್ ವಾಲ್ಸ್ ಬಲವು ಕ್ರಮೇಣ ಮೈಕೆಲ್ಗಳನ್ನು ಒಟ್ಟಿಗೆ ತರುತ್ತದೆ ಮತ್ತು ಗಾತ್ರ ಮತ್ತು ಆಕಾರದ ಅಸಿಮ್ಮೆಟ್ರಿಯ ಕಾರಣದಿಂದಾಗಿ ಬೌಂಡ್ ವಾಟರ್ ಲೇಯರ್ ನೆಟ್ವರ್ಕ್ ರಚನೆಯನ್ನು ರೂಪಿಸುತ್ತದೆ.ಫೈಬ್ರಸ್ CMC ನೆಟ್ವರ್ಕ್ ರಚನೆಯು ದೊಡ್ಡ ಪರಿಮಾಣ, ಬಲವಾದ ಅಂಟಿಕೊಳ್ಳುವಿಕೆಯನ್ನು ಹೊಂದಿದೆ ಮತ್ತು ಮೆರುಗು ದೋಷಗಳನ್ನು ಕಡಿಮೆ ಮಾಡುತ್ತದೆ.
ಲೆವಿಟೇಶನ್ ಪರಿಣಾಮ
ಸೇರ್ಪಡೆಗಳಿಲ್ಲದೆಯೇ, ಕಾಲಾನಂತರದಲ್ಲಿ ಗುರುತ್ವಾಕರ್ಷಣೆಯ ಕಾರಣದಿಂದಾಗಿ ಮೆರುಗು ಸ್ಲರಿ ನೆಲೆಗೊಳ್ಳುತ್ತದೆ ಮತ್ತು ಇದು ಸಂಭವಿಸುವುದನ್ನು ತಡೆಯಲು ನಿರ್ದಿಷ್ಟ ಪ್ರಮಾಣದ ಜೇಡಿಮಣ್ಣನ್ನು ಸೇರಿಸುವುದು ಸಾಕಾಗುವುದಿಲ್ಲ.ಆದಾಗ್ಯೂ, ನಿರ್ದಿಷ್ಟ ಪ್ರಮಾಣದ CMC ಯ ಸೇರ್ಪಡೆಯು ಮೆರುಗು ಅಣುಗಳ ಗುರುತ್ವಾಕರ್ಷಣೆಯನ್ನು ಬೆಂಬಲಿಸುವ ಒಂದು ಜಾಲಬಂಧ ರಚನೆಯನ್ನು ರಚಿಸಬಹುದು.CMC ಅಣುಗಳು ಅಥವಾ ಅಯಾನುಗಳು ಗ್ಲೇಸುಗಳಲ್ಲಿ ವಿಸ್ತರಿಸುತ್ತವೆ ಮತ್ತು ಜಾಗವನ್ನು ಆಕ್ರಮಿಸುತ್ತವೆ, ಮೆರುಗು ಅಣುಗಳು ಮತ್ತು ಕಣಗಳ ಪರಸ್ಪರ ಸಂಪರ್ಕವನ್ನು ತಡೆಯುತ್ತದೆ, ಇದು ಸ್ಲರಿಯ ಆಯಾಮದ ಸ್ಥಿರತೆಯನ್ನು ಸುಧಾರಿಸುತ್ತದೆ.ನಿರ್ದಿಷ್ಟವಾಗಿ ಹೇಳುವುದಾದರೆ, ಋಣಾತ್ಮಕವಾಗಿ ಚಾರ್ಜ್ ಮಾಡಲಾದ CMC ಅಯಾನುಗಳು ಋಣಾತ್ಮಕವಾಗಿ ಚಾರ್ಜ್ ಮಾಡಲಾದ ಮಣ್ಣಿನ ಕಣಗಳನ್ನು ಹಿಮ್ಮೆಟ್ಟಿಸುತ್ತದೆ, ಇದು ಮೆರುಗು ಸ್ಲರಿಯ ಹೆಚ್ಚಿನ ಅಮಾನತುಗೆ ಕಾರಣವಾಗುತ್ತದೆ.ಇದರರ್ಥ CMC ಮೆರುಗು ಸ್ಲರಿಯಲ್ಲಿ ಉತ್ತಮ ಅಮಾನತು ಹೊಂದಿದೆ.CMC ಯಿಂದ ರೂಪುಗೊಂಡ ನೆಟ್ವರ್ಕ್ ರಚನೆಯು ಮೆರುಗು ದೋಷಗಳನ್ನು ಕಡಿಮೆ ಮಾಡಲು ಮತ್ತು ಮೃದುವಾದ ಮೇಲ್ಮೈ ಮುಕ್ತಾಯವನ್ನು ಖಚಿತಪಡಿಸಿಕೊಳ್ಳಲು ಸಹಾಯ ಮಾಡುತ್ತದೆ.ಒಟ್ಟಾರೆಯಾಗಿ, ಮೆರುಗು ಪ್ರಕ್ರಿಯೆಯಲ್ಲಿ ಸ್ಥಿರವಾದ ಮತ್ತು ಉತ್ತಮ-ಗುಣಮಟ್ಟದ ಫಲಿತಾಂಶಗಳನ್ನು ಸಾಧಿಸಲು ಮುಖ್ಯವಾದ ಮೆರುಗು ಸ್ಲರಿಯ ಸ್ಥಿರತೆ ಮತ್ತು ಅಮಾನತುಗೊಳಿಸುವಿಕೆಯಲ್ಲಿ CMC ನಿರ್ಣಾಯಕ ಪಾತ್ರವನ್ನು ವಹಿಸುತ್ತದೆ.
CMC ಅನ್ನು ಆಯ್ಕೆಮಾಡುವಾಗ ಪರಿಗಣಿಸಬೇಕಾದ ಪ್ರಶ್ನೆಗಳು
ಮೆರುಗು ಉತ್ಪಾದನೆಯಲ್ಲಿ CMC ಯ ಸರಿಯಾದ ಬಳಕೆಯು ಅಂತಿಮ ಉತ್ಪನ್ನದ ಗುಣಮಟ್ಟವನ್ನು ಹೆಚ್ಚು ಸುಧಾರಿಸುತ್ತದೆ.ಉತ್ತಮ ಪರಿಣಾಮವನ್ನು ಖಚಿತಪಡಿಸಿಕೊಳ್ಳಲು, ಅನುಸರಿಸಲು ಹಲವಾರು ಪ್ರಮುಖ ಅಂಶಗಳಿವೆ.ಮೊದಲನೆಯದಾಗಿ, ಖರೀದಿಸುವ ಮೊದಲು CMC ಮಾದರಿಯ ವಿವರಣೆಯನ್ನು ಪರಿಶೀಲಿಸುವುದು ಮತ್ತು ಉತ್ಪಾದನೆಗೆ ಸೂಕ್ತವಾದ ವಿವರಣೆಯನ್ನು ಆರಿಸುವುದು ಮುಖ್ಯವಾಗಿದೆ.ಮಿಲ್ಲಿಂಗ್ ಸಮಯದಲ್ಲಿ ಮೆರುಗುಗೆ CMC ಅನ್ನು ಸೇರಿಸಿದಾಗ, ಇದು ಮಿಲ್ಲಿಂಗ್ ದಕ್ಷತೆಯನ್ನು ಸುಧಾರಿಸಲು ಸಹಾಯ ಮಾಡುತ್ತದೆ.ಗರಿಷ್ಠ ಪರಿಣಾಮವನ್ನು ಸಾಧಿಸಲು ನೀರನ್ನು ಸುರಿಯುವಾಗ ನೀರು-ಸಿಎಂಸಿ ಅನುಪಾತಕ್ಕೆ ಸಹ ಗಮನ ನೀಡಬೇಕು.
ಮೆರುಗು ಸ್ಲರಿ ಸಾಕಷ್ಟು ಸ್ಥಿರವಾಗಿದೆ ಮತ್ತು CMC ಉತ್ತಮ ಪರಿಣಾಮವನ್ನು ವಹಿಸುತ್ತದೆ ಎಂದು ಖಚಿತಪಡಿಸಿಕೊಳ್ಳಲು ಒಂದು ದಿನ ಅಥವಾ ಎರಡು ದಿನಗಳವರೆಗೆ ಕೊಳೆಯಲು ಅನುಮತಿಸಬೇಕು.ಕಾಲೋಚಿತ ಬದಲಾವಣೆಗಳಿಗೆ ಅನುಗುಣವಾಗಿ ಸೇರಿಸಲಾದ CMC ಯ ಪ್ರಮಾಣವನ್ನು ಸರಿಯಾಗಿ ಹೊಂದಿಸುವುದು ಮುಖ್ಯವಾಗಿದೆ, ಬೇಸಿಗೆಯಲ್ಲಿ ಹೆಚ್ಚು ಸೇರಿಸಲಾಗುತ್ತದೆ, ಚಳಿಗಾಲದಲ್ಲಿ ಕನಿಷ್ಠ, ಮತ್ತು ನಡುವೆ 0.05% ರಿಂದ 0.1% ವರೆಗೆ ಇರುತ್ತದೆ.ಚಳಿಗಾಲದಲ್ಲಿ ಡೋಸೇಜ್ ಬದಲಾಗದೆ ಉಳಿದಿದ್ದರೆ, ಇದು ಸ್ರವಿಸುವ ಮೆರುಗು, ನಿಧಾನ ಒಣಗಿಸುವಿಕೆ ಮತ್ತು ಜಿಗುಟಾದ ಮೆರುಗುಗೆ ಕಾರಣವಾಗಬಹುದು.ಇದಕ್ಕೆ ವಿರುದ್ಧವಾಗಿ, ಸಾಕಷ್ಟು ಡೋಸೇಜ್ ದಟ್ಟವಾದ ಮತ್ತು ಒರಟಾದ ಮೆರುಗು ಮೇಲ್ಮೈಗೆ ಕಾರಣವಾಗುತ್ತದೆ.
ಬೇಸಿಗೆಯಲ್ಲಿ, ಬ್ಯಾಕ್ಟೀರಿಯಾದ ಪ್ರಭಾವದಿಂದಾಗಿ ಹೆಚ್ಚಿನ ತಾಪಮಾನವು CMC ಯ ಸ್ನಿಗ್ಧತೆಯನ್ನು ಕುಗ್ಗಿಸಬಹುದು.ಆದ್ದರಿಂದ, ವಿರೋಧಿ ತುಕ್ಕು ಕೆಲಸವನ್ನು ನಿರ್ವಹಿಸುವುದು ಮತ್ತು CMC ಗುಣಮಟ್ಟವನ್ನು ಕಾಪಾಡಿಕೊಳ್ಳಲು ಸೂಕ್ತವಾದ ಸೇರ್ಪಡೆಗಳನ್ನು ಸೇರಿಸುವುದು ಅವಶ್ಯಕ.ಅಂತಿಮವಾಗಿ, ಗ್ಲೇಸುಗಳನ್ನೂ ಬಳಸುವಾಗ, ದಹನದ ಸಮಯದಲ್ಲಿ CMC ಯ ಶೇಷವು ಮೆರುಗು ಮೇಲ್ಮೈ ಮೇಲೆ ಪರಿಣಾಮ ಬೀರುವುದನ್ನು ತಡೆಯಲು 100 ಜಾಲರಿಗಿಂತ ಹೆಚ್ಚಿನ ಜರಡಿಯಿಂದ ಅದನ್ನು ಜರಡಿ ಮಾಡಲು ಸೂಚಿಸಲಾಗುತ್ತದೆ.ಈ ಮಾರ್ಗಸೂಚಿಗಳನ್ನು ಅನುಸರಿಸುವ ಮೂಲಕ, ಉತ್ಪನ್ನದ ಗುಣಮಟ್ಟವನ್ನು ಸುಧಾರಿಸಲು CMC ಅನ್ನು ಮೆರುಗು ಉತ್ಪಾದನೆಯಲ್ಲಿ ಪರಿಣಾಮಕಾರಿಯಾಗಿ ಬಳಸಬಹುದು.
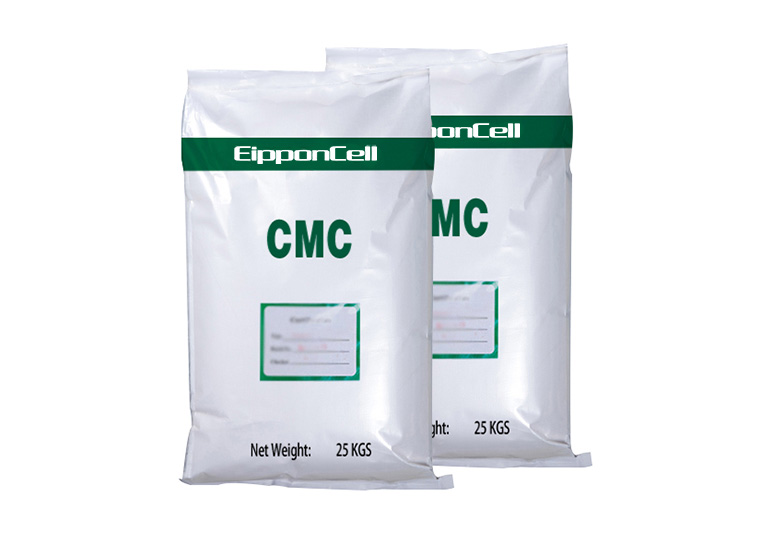